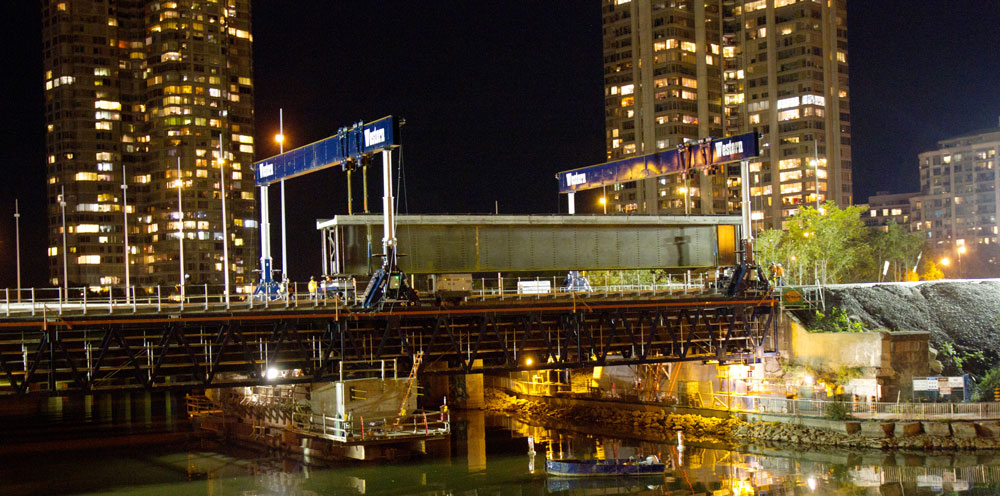
When leading Canadian heavy lift contractor, Western Mechanical, was asked to assist in the replacement of the Humber River railroad bridge it selected an Enerpac hydraulic gantry for the precision lifting and replacement of bridge spans over an 8-week period.
A Canadian Crown agency manages and integrates road and public transport in the Golden Horseshoe region, including the cities of Toronto and Hamilton and area, in the province of Ontario. Earlier this year the agency undertook a major project to refurbish six century-old bridges on GO Transit’s 01 Lakeshore West line, one of the seven train lines of the GO Transit system in the Greater Toronto Area, Ontario.
Working for main contractor, Soncin Construction, Western Mechanical was charged with replacing eight bridge spans on the Humber Bay railroad bridge crossing the mouth of the Humber River, south of The Queensway and north of Lake Shore Boulevard and the Gardiner Expressway, in downtown Toronto.
Originally constructed in 1911 for the Grand Trunk Railway, the bridge’s steel girder system and concrete substructure well reflected the engineering techniques of the early-twentieth century, however, the 107-year-old bridge had run its course. According to the Crown agency, “The bridge was approaching the end of its life cycle and required some much needed repairs.” They wished to replace and raise the bridge’s steel spans to bring the structure to a good state of repair, improve the vertical clearance to the river and renew the waterproofing system, over an 8-week period. Given the critical role of the bridge, the rail line had to remain open to local traffic during weekdays and could only be closed for bridge work during a 50-hour work block at the weekends.
The Humber River four-track railway bridge comprises steel plate girders spanning a concrete substructure. Two spans are carried by a central stone pier and abutments, which incorporate portions of the nineteenth century stone abutments that supported the previous Great Western Railway bridge. Over time the bridge had settled about 800 mm so a second helper pier was installed to help support the bridge some 75 years prior. The construction of the bridge as two spans per rail line meant that a pair of spans could be changed out at a time during a single work block. Each span section weighed 400 ton and was 100 ft long, 12-17 ft wide and 9 ft high.
Western Mechanical opted to use its new Enerpac SBL1100 telescopic hydraulic gantry rather than a crane for the project. “The gantry is ideal for this type of heavy lift where you are handling a long heavy structure. Using a crane would have been expensive especially since we’d only be using it at the weekends,” says Rob Doucet, project manager for the Heavy Lift Division of Western Mechanical.
Western Mechanical’s challenge was to lift the old bridge span clear of the bridge and then install the new span without placing any excessive load on the partly deconstructed bridge. To achieve this, the company installed its deep truss gantry track system running parallel to the bridge and on either side, but independent of the bridge itself. Western’s track system was supported on new additions made to the two existing piers and at each abutment. This approach relied on using a gantry header beam that was wider than the width of the bridge.
“We needed a header beam 24 meters in length, which is far longer than we’ve used on past project lifts. Working with Western Mechanical’s engineering department, Enerpac provided full engineering support enabling us to confidently proceed with our lift strategy. Given the length of the header beam and load distribution Enerpac recommended a wider header beam and modifications to the swivel interface where the header beam rests on the top of each gantry leg,” notes Rob Doucet.
With the gantry in place, Western Mechanical could begin the job of removing the span sections. Each steel span configuration was DPG (dual plate girder) style construction with an upper precast concrete panel deck. The top concrete deck of the bridge included a steel I-beam section creating significantly higher weight in the upper part of the span, making it top-heavy with a high center of gravity. This wasn’t the only challenge of the lift that needed to be overcome, Doucet noted. “We found that the spans were not linear and were skewed by about 3 degrees, also the East end sections had previously settled by 800 mm at the abutment. We had to level this using rail ballast before installing the new span sections.” By using the gantry, the spans could be precisely lifted in this skewed state and held aloft while cribbing was installed below to correct the angle.

In selecting the Enerpac SBL1100 gantry system for this lift, Western Mechanical maximized the freedom of movement offered by the telescopic gantry comments Doucet again, “The telescopic legs meant we had the vertical movement to lift the span section clear of the bridge itself. The gantry’s independent track system running the length of the bridge gave us east-to-west movement parallel to the bridge providing us the ability to utilize Enerpac’s independent motorised gantry leg rollers saving time to reset for the next adjacent span lift. An integral component to the system was the Enerpac header beam and powered side shift beam traveller units. With a 1500 kN capacity these units allowed us to move the lifted span from north-to-south perpendicular to the tracks and onto awaiting rail flatcars to be loaded out to the demolition yard. The process was reversed for installing the new spans.”
Using the SBL1100 gantry system provided many advantages over traditional cranes. The primary advantage was the controlled movement in the x, y, and z axes, all while being controlled from Enerpac’s body-worn, RF (radio frequency) remote pendent and information center providing operators with real time load-weight and position during the entire lift process. Another advantage was the modularity of the lifting system. Enerpac’s gantry components could be easily transported by rail to site and their lightweight enabled the use of a smaller crane for assembly which was completed ahead of schedule. All gantry operations were controlled using the lifting system’s wireless controller, allowing the operator unrestricted views and automatic synchronization for lifting/lowering and traveling. This controlled movement, along with the gantry’s ability to accurately measure the weight of the spans improved the safety of the lifts. Another safety feature was the ability to mechanically lock the header beam and gantry legs in place, allowing rail clearance for train traffic to flow beneath during the week.
Western Mechanical completed the Humber River railroad bridge project over the allotted 8 50-hour weekend work blocks. It was allowed 26 of the 50 hours during the work block to perform their scope of work. Including Enerpac as an integral team member on this project and Western’s decision to use the SBL1100 system was the right choice, allowing Western to finish all of the major weekend work blocks safely ahead of schedule. By the end of the project, Western able to set a new record for completing their scope of work in just 21 hours.
By adding the Enerpac’s SBL1100 to Western Mechanical’s fleet of equipment, Western will continue to realize improvements to project cost, safety, reliability and be capable of heavier and larger gantry lifts than before.
For more information on Enerpac and its range of hydraulic gantries, visit www.enerpac.com.